Steel back plate is an important part of brake pads. The main function of the brake pad steel back plate is to fix the friction material and facilitate its installation on the brake system. In most modern cars, especially those that use disc brakes, high-strength friction materials are usually bonded onto a steel plate, which is called a back plate. The back plate is usually designed with rivets and holes for installing brake pads on the caliper. In addition, the material of the steel back is usually thicker and the process is complex to ensure that it can withstand the enormous pressure and heat generated during the braking process.
Punching machine and Laser cutting production are two different processing methods for back plate, but which one is better for modern back plate production? Actually the choice of method depends on specific processing requirements, material characteristics, budget, and production goals.
Punching machine type:
Using punching machine to make back plate is most traditional method. The main work flow is as below:
1.1 Plate cutting:
The size of the purchased steel plate may not be suitable for punching blanking, thus we would use Plate shearing machine to cut the steel plate into suitable size first.
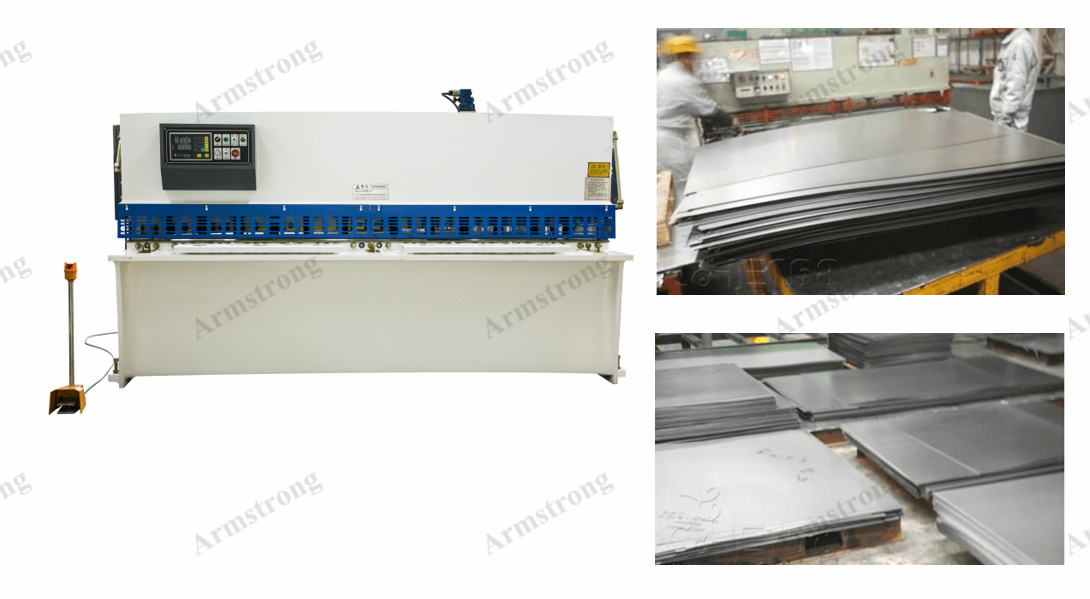
Plate shearing machine
1.1 Blanking:
Install the stamping die on punching machine, and blank the back plate from steel plate. We can install the Automatic feeding device beside punching machine, thus punching machine can continuously blank the steel plate.
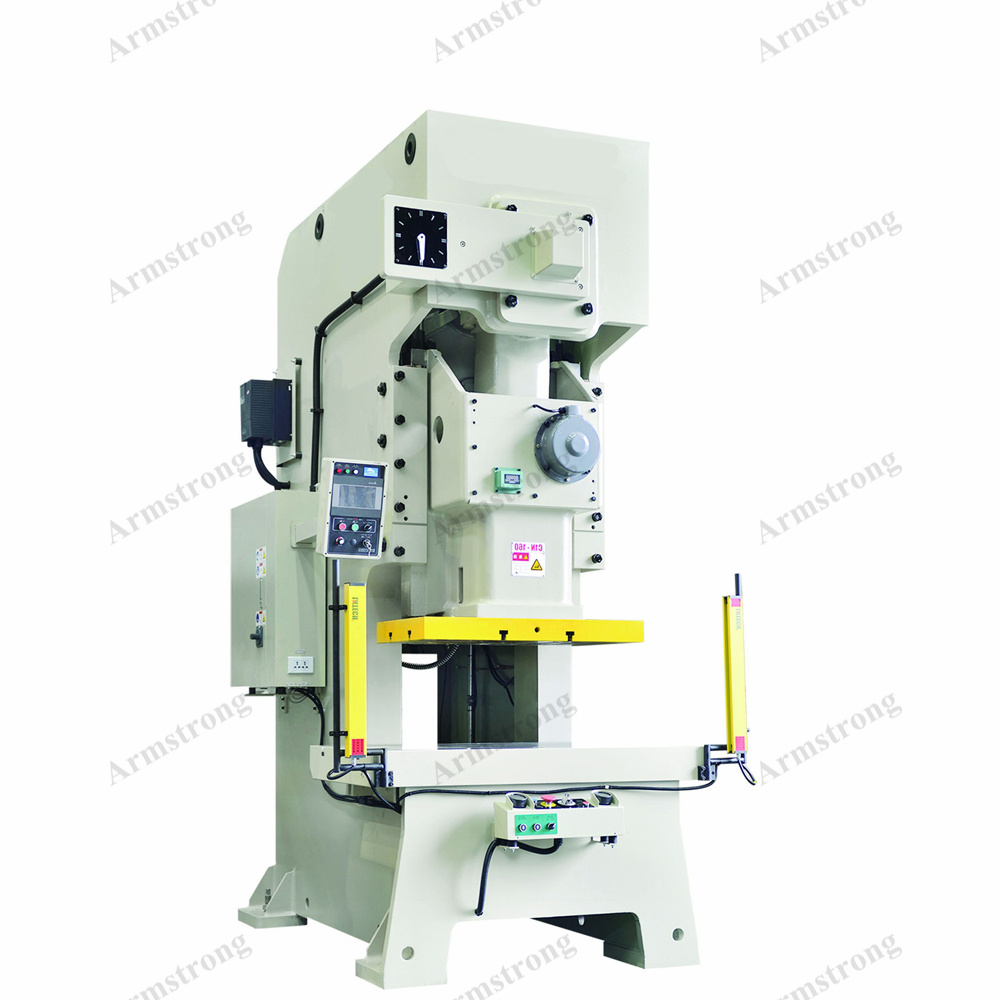
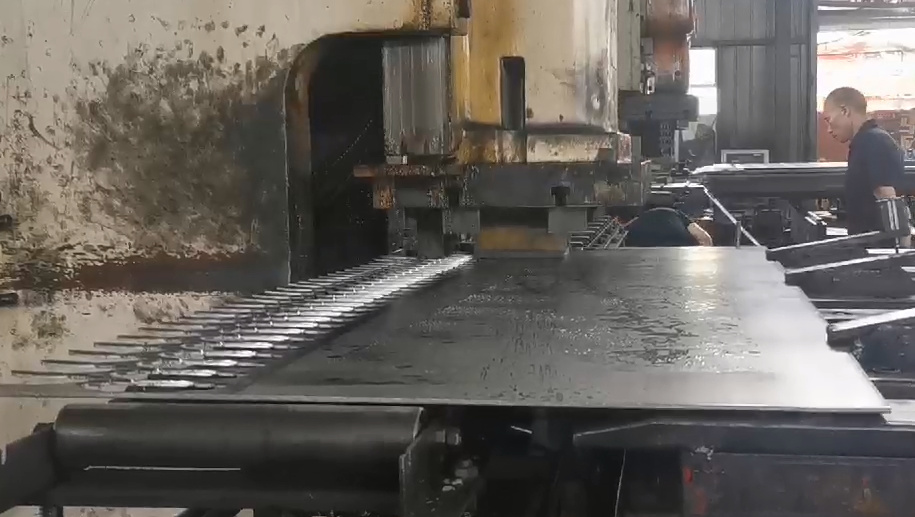
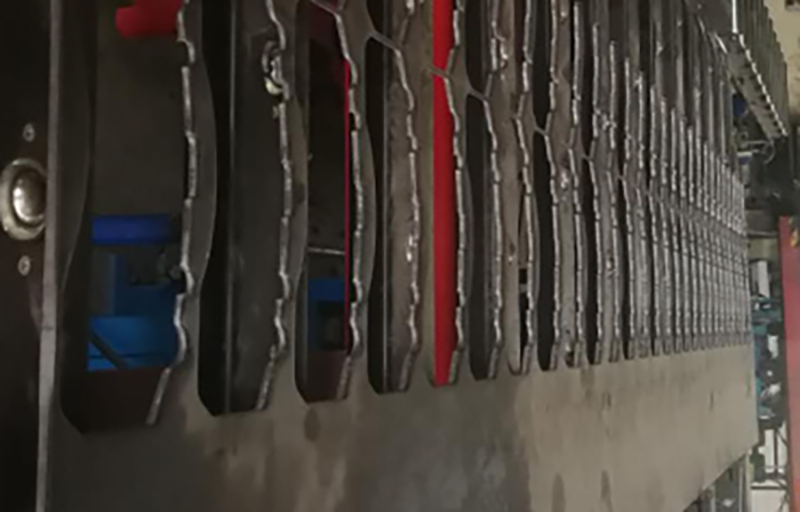
Blank from steel plate
1.1 Press holes / pins:
For passenger car back plate, it normally has pins or holes to increase the shear strength. For commercial vehicle, part of back plates also have holes. Thus we need to use punching machine and press holes or pins.
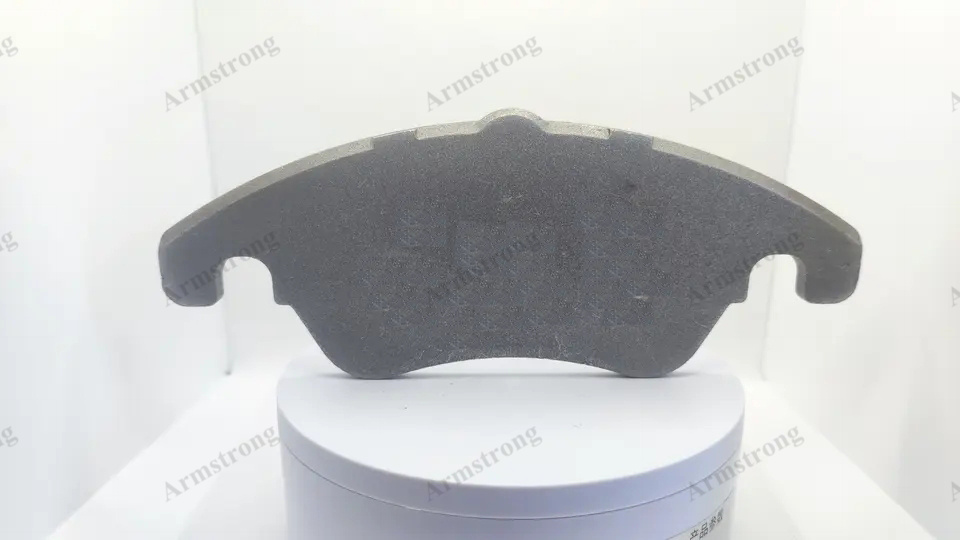
After blanking
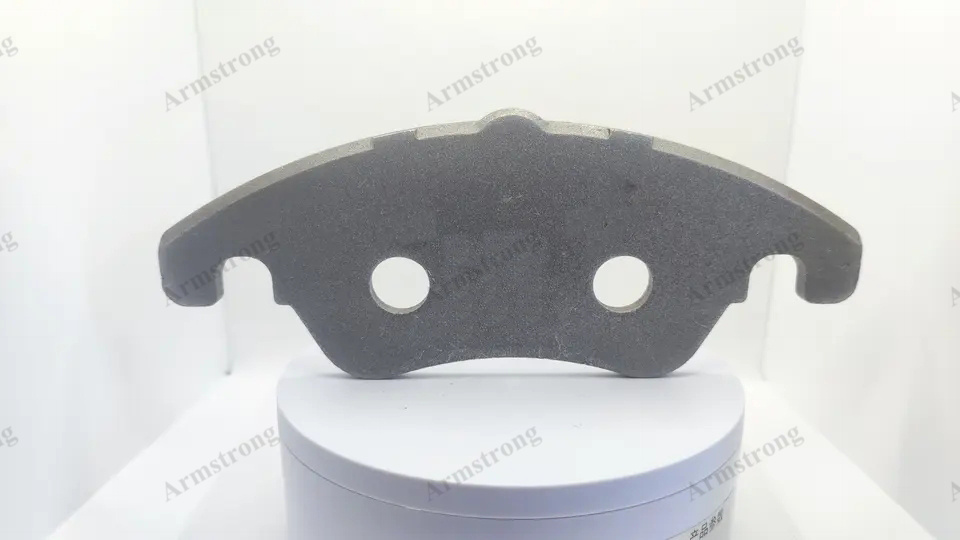
Press holes
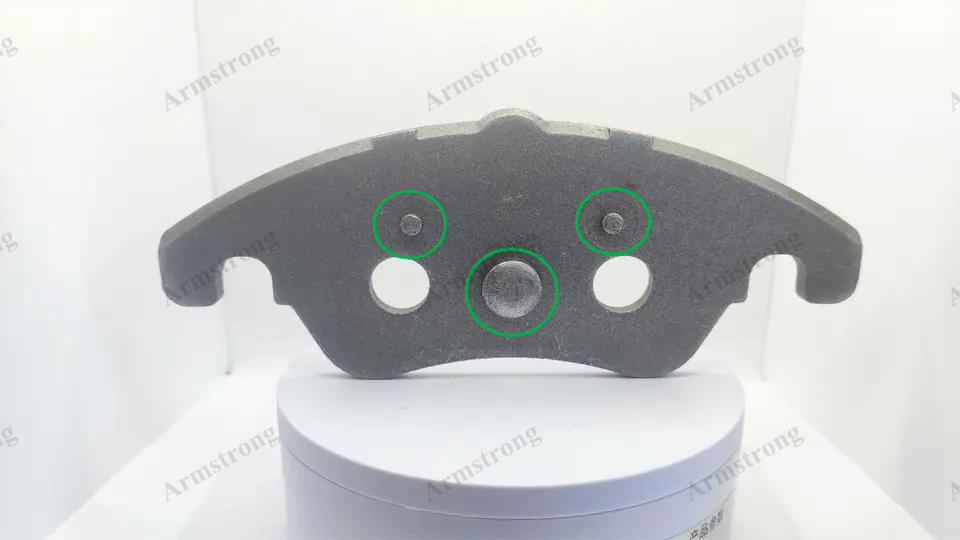
Press pins
1.1 Fine cut:
For passenger car back plate, to make the back plate assemble in caliper smoothly and has better appearance, it will fine cut the edge.
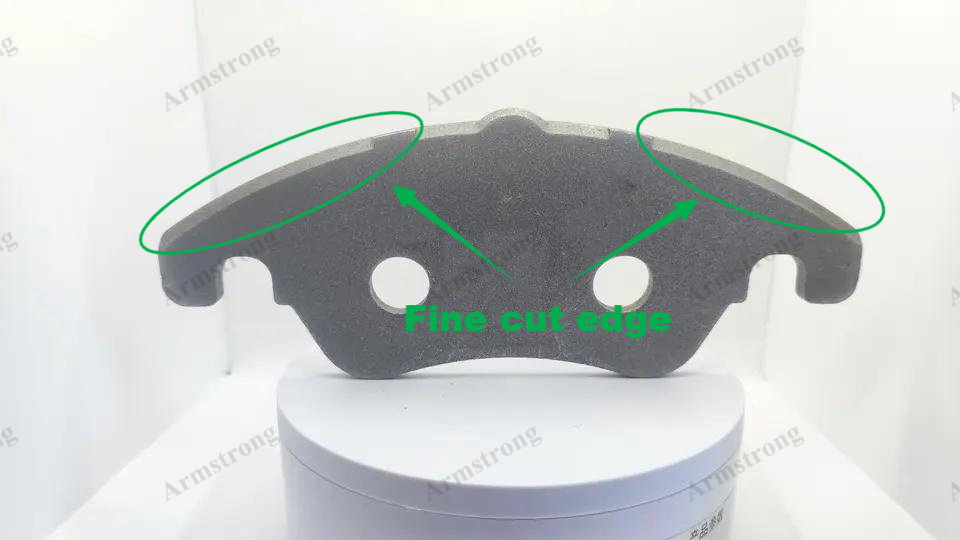
1.1 Flattening:
After pressing so many times by different stamping dies, especially the fine cut process, the back plate will have expansion and deformation. To ensure the back plate assemble size and flatness, we’ll add flattening process. This is the last step on punching machine.
1.2 Deburring:
The edge of back plate is prone to burrs after stamping, thus we’ll use Deburring machine to remove these burrs.
Advantages:
1.The traditional punching machine type production efficiency is very high, suitable for mass production. The back plate consistency is good.
Disadvantages:
1.The whole production line requests 3-4 punching machines at least, for different process the punching machine pressure is also different. For example, PC back plate blanking need 200T punching machine, CV back plate blanking need 360T-500T punching machine.
2.For one back plate production, the different process need 1 set of stamping die. All stamping dies need to check and maintenance after a period of use.
3.Several punching machine work simultaneously makes a lot of noise, workers who work under loud noise for a long time will do harm to their hearing.
1.Laser cutting type:
1.1 Laser cut:
Put the steel plate on laser cutting machine , the requirements for steel plate size are not strict. Just make sure the Steel plate size is within Max. machine request. Pls note the laser cutter power and cutting ability, PC back plate thickness is normally within 6.5mm, CV back plate thickness is within 10mm.
Input the back plate drawing into laser cutter control computer, the cutting amount and layout can be randomly designed by operator.
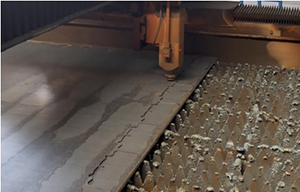
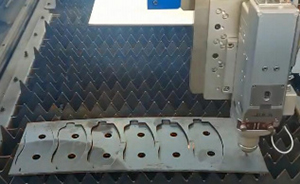
1.1 Fine processing on machining center:
The laser cutting machine can only cut the back plate shape and holes, but each piece will have a starting point on the back plate edge. In addition, the cutting size need to be checked. Thus we would use machining center
to fine process the back plate edge, and also make chamfer on PC back plate. (same function as Fine cut).
1.1 Make pins:
Though the laser cutting machine can make back plate outer size, we still need one punching machine to press the pins on back plate.
1.2 Deburring:
Laser cutting will also have burrs on back plate edge, thus we suggest to use deburring machine to remove the burrs.
Advantages:
1.No need many stamping dies for one model, save the stamping die development cost.
2.Operator can cut different models on one steel sheet, very flexible and high efficiency. It’s very convenient for sample or small batch back plate production.
Disadvantages:
1. Efficiency is much lower than punching machine type.
For 3kw dual platform laser cutter,
PC back plate: 1500-2000 pcs/8hrs
CV back plate: 1500 pcs/8hrs
1.For small size back plate which width and length smaller than support strip, the back plate is easily raised and hit the laser cut head.
2.To ensure the edge cut appearance, need to use oxygen for cutting. It’s a consumables item for back plate cutting.
Summary:
Both punching machine and laser cutting machine can produce qualified back plate, customer can choose which one solution is better based on production capacity, budget and actual technical ability.
Post time: Jun-21-2024